Identifying the quality of a coated aluminum coil involves a careful assessment of various factors that contribute to its performance, durability, and overall value. Coated aluminum coils are widely used in construction, transportation, and other industries for their aesthetic appeal, corrosion resistance, and protection. Here are some key aspects to consider when evaluating the quality of a coated aluminum coil:
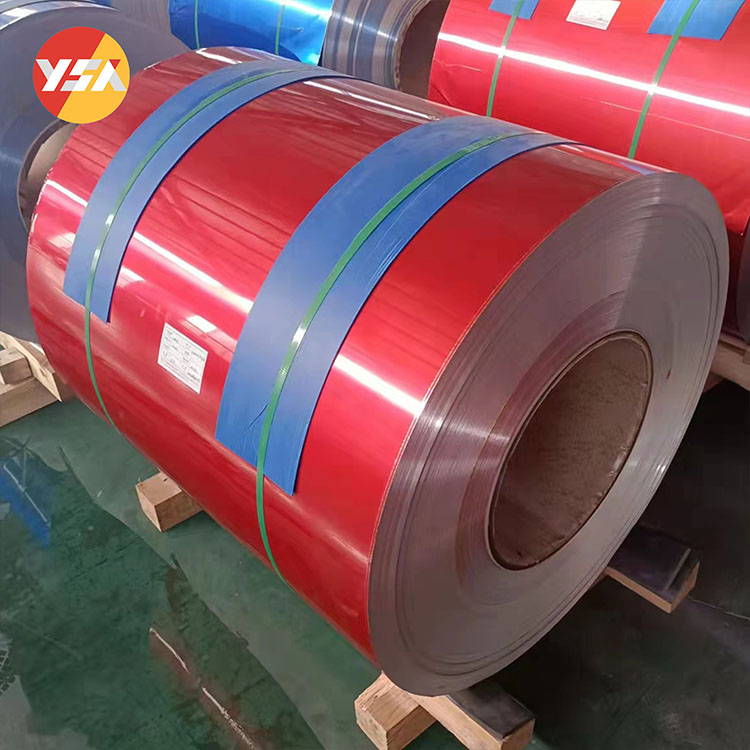
- Coating Type and Composition:
- Determine the type of coating used on the aluminum coil. Common coatings include polyester, polyurethane, fluorocarbon (PVDF), and epoxy. Each type offers different levels of durability, UV resistance, and color retention.
- Inquire about the coating composition and thickness. A higher-quality coil will often have a well-applied, uniform coating that meets industry standards.
- Surface Finish:
- Examine the coil’s surface for consistency and smoothness. A high-quality coil will have an even finish without visible defects like bubbles, scratches, or uneven color distribution.
- Check for uniform gloss and sheen across the entire coil.
- Color Consistency:
- If the coil comes in a specific color, assess the color consistency throughout the entire coil and across different batches. Variations in color could indicate an inferior coating or manufacturing process.
- Adhesion and Flexibility:
- Test the adhesion of the coating by performing a crosshatch adhesion test. Use a sharp blade to create a grid of small squares on the coated surface and apply adhesive tape over it. Pull off the tape; if the coating remains intact, it signifies good adhesion.
- Evaluate the flexibility of the coated aluminum by bending a sample piece. A high-quality coating should maintain its integrity without cracking or flaking.
- Corrosion Resistance:
- Coated aluminum is often chosen for its corrosion resistance. Inquire about the coating’s ability to withstand exposure to harsh environmental conditions, such as saltwater, pollutants, and acidic substances.
- Look for certifications or testing data that demonstrate the coil’s corrosion resistance properties.
- Weatherability and UV Resistance:
- Coated aluminum coils used for outdoor applications should possess good weatherability and UV resistance. Inquire about the coil’s ability to retain color and appearance when exposed to sunlight and weathering over time.
- Warranty and Certifications:
- A reputable supplier will often provide a warranty for their coated aluminum coils. Check the warranty period and terms to ensure they align with your expectations.
- Look for relevant certifications or standards compliance, such as AAMA (American Architectural Manufacturers Association) or ASTM (American Society for Testing and Materials) standards.
- Supplier Reputation:
- Research the supplier’s reputation and industry standing. Established and well-regarded suppliers are more likely to provide high-quality coated aluminum coils.
- Samples and Testing:
- Request samples of the coated aluminum coil and conduct your own tests to evaluate its adhesion, flexibility, color retention, and corrosion resistance.
- If feasible, collaborate with a testing laboratory to perform comprehensive tests on the coated coil to assess its quality based on industry standards.
- Customer Reviews and References:
- Seek feedback from previous customers or references who have used the same coated aluminum coil. Their experiences can provide valuable insights into the coil’s performance and longevity.
In conclusion, identifying the quality of a coated aluminum coil requires a comprehensive assessment of its coating type, surface finish, color consistency, adhesion, corrosion resistance, weatherability, certifications, and supplier reputation. By considering these factors and conducting thorough testing, you can make an informed decision and select a coated aluminum coil that meets your specific needs and quality standards.