In the sophisticated world of pharmaceutical packaging, the safety and efficacy of every tablet and capsule are maintained by the protection of multiple barriers. Among them, the seemingly inconspicuous silver sealing foil at the top of the blister package is the ultimate guardian of moisture, oxygen, light and external pollutants. 8011 aluminum foil roll, with its balanced and excellent characteristics, has become the benchmark choice in the field of pharmaceutical foil applications.
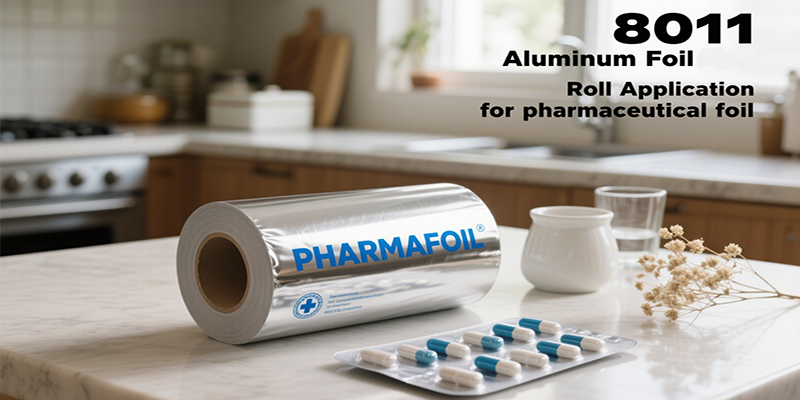
The core mission of pharmaceutical foil
Pharmaceutical foil is not an ordinary packaging material. Its performance is directly related to the quality of medicines and patient safety, and it carries an uncompromising core mission.
- Ultimate barrier property: This is the lifeline of pharmaceutical foil. It must effectively isolate the intrusion of water vapor, oxygen, light, and external microorganisms, odors and pollutants.
- Excellent sealing: It must be able to form a firm, long-lasting, leak-free heat seal with common pharmaceutical blister materials such as PVC, PVDC, and cold stamped aluminum. Any minor sealing defects may cause the drug to fail.
- Excellent mechanical properties: It must have sufficient tensile strength, elongation and toughness to withstand the processing stresses of stamping, stretching, heat sealing and other processing of high-speed automatic blister packaging machines, as well as physical impacts during subsequent transportation and storage to avoid cracking or perforation.
- Purity, safety and compliance: Direct or indirect contact with drugs must comply with the world’s most stringent pharmaceutical packaging regulations. The material itself must be pure and non-toxic, without any substances that may migrate to drugs and endanger the health of patients, and the production process must be highly clean.
- It must adapt to the continuous and stable operation of high-speed automated packaging lines and have good printing suitability, coating suitability, slitting and rewinding performance and molding performance.
Features of 8011 aluminum foil roll
Among many aluminum foil alloy grades, 8011 aluminum alloy perfectly meets the stringent requirements of pharmaceutical foil for the base material due to its unique composition design and processing technology.
Pure material, safe and reliable
- High purity basis: 8011 belongs to aluminum-iron-silicon alloy, and its basic aluminum purity is extremely high. The content of impurity elements such as copper, zinc, and manganese is strictly controlled to ensure the purity of the final foil.
- Safety and non-toxic guarantee: After strict smelting, casting and refining processes, combined with subsequent cold rolling, annealing and other process controls, the risk of possible harmful substances precipitation is effectively eliminated or solidified, meeting the highest safety standards for food and drug contact materials.
Excellent barrier performance
Aluminum foil itself has a unique and nearly perfect barrier property of metal materials, and has a zero-level transmittance for gas, water vapor, light, and microorganisms. Through precision rolling, 8011 aluminum foil minimizes pinhole defects while achieving the required thickness, ensuring its absolute effectiveness as a core barrier layer. Even a micron-thick aluminum foil layer can provide unparalleled protection.
Balanced excellent mechanical properties
- Balance of strength and toughness: 8011 alloy can obtain an ideal combination of high strength and medium elongation through cold work hardening and appropriate annealing process. This allows 8011 aluminum foil rolls to withstand the stretching and impact during high-speed packaging, while maintaining sufficient toughness to avoid brittle cracking during forming and subsequent processing.
- Thickness uniformity: High-quality 8011 aluminum foil rolls have extremely precise thickness tolerance control. This is crucial to ensure the temperature uniformity and pressure transmission consistency of the sealing foil during high-speed heat sealing, which directly affects the final sealing strength and sealing integrity.
Excellent processing adaptability
- Flatness and plate shape: Good plate shape is the basis for high-speed and stable operation. The excellent plate shape control of 8011 aluminum foil rolls reduces wrinkling, deviation and other problems during unwinding, coating, printing, laminating and slitting.
- Surface characteristics: The surface cleanliness of 8011 aluminum foil is high and the roughness is controllable, which provides an ideal adhesion basis for its subsequent coating or printing. YSA Aluminum can customize 8011 aluminum foil rolls with different surface treatment states according to the specific needs of customers’ downstream processing technology to optimize your coating or printing effect.
- Slitting and rewinding quality: Aluminum foil rolls with neat edges, no burrs, uniform winding tension and flat end faces are the key to ensuring stable unwinding and reducing belt breakage on customers’ high-speed laminating or printing equipment.
The 8011 aluminum foil rolls produced by YSA Aluminum control purity from the source and provide complete material certification and compliance declaration. The use of advanced rolling and online monitoring technology ensures that the 8011 aluminum foil rolls it provides have industry-leading thickness uniformity and dimensional stability. Lay a solid foundation for the compliance of your pharmaceutical packaging materials and safeguard your continuous and efficient production.
Analysis of the structure of pharmaceutical foil: 8011 aluminum foil roll as the core substrate
Modern pharmaceutical foil is usually a multi-layer composite material, with 8011 aluminum foil roll as the core substrate, constituting its main structure.
- 1. Printing layer/protective layer: the outermost layer, used to print drug information, brand logo, etc., sometimes covered with protective paint.
- 2. Core barrier layer: that is, 8011 aluminum foil roll with a thickness of 20-40 microns, providing absolute water vapor, oxygen, and light barrier.
- 3. Heat seal adhesive layer: coated on the side of the aluminum foil facing the blister base plate, usually a specially formulated polyolefin adhesive. Under the heating and pressure of the heat seal plate, this adhesive layer melts and firmly bonds to the blister base plate to form a seal. The clean and activated surface of 8011 aluminum foil is the basis for good wetting and firm adhesion of the heat seal adhesive.
- 4. Adhesive layer: If the aluminum foil needs to be compounded with other functional films, an adhesive layer needs to be added.
How to choose 8011 aluminum foil roll for pharmaceutical foil production
As a pharmaceutical foil manufacturer, when choosing 8011 aluminum foil roll raw materials, special attention should be paid to the following core indicators.
- Thickness and tolerance: Accurate and consistent thickness is the basis for ensuring stable barrier properties and processing performance. Common thicknesses such as 0.020mm, 0.025mm, 0.030mm, etc., require strict tolerances.
- Consistency of mechanical properties: small differences between batches such as tensile strength and elongation, ensuring stable parameters of high-speed production lines.
- Surface properties: cleanliness, wetting tension (dyne value, usually required to be >32 dynes/cm or even higher to ensure coating and printing adhesion), surface defects (strictly control pinholes, bright spots, dark spots, scratches, indentations, etc.).
- Coil quality: precise roll diameter, width, and tube core size; neat winding and uniform tension; flat end surface without tower shape or elastic edge; no joints or joints are firm and clearly marked.
- Cleanliness and low migration: Comply with the relevant regulations on pharmaceutical packaging materials, and provide complete material safety declarations and compliance certificates (such as RoHS, REACH, FDA, EU 10/2011, etc.). The supplier’s clean production environment and strict quality control system are important guarantees.
- Batch stability and traceability: The performance of different batches of raw materials is highly consistent, and a complete production batch traceability system is available.
As your trusted aluminum foil raw material partner, ysa Aluminum is always committed to providing you with high-quality 8011 aluminum foil roll substrates with strict process standards, stable product performance and complete compliance support to jointly protect life and health.
Ysa 8011 aluminum foil roll helps build a reliable supply chain for pharmaceutical packaging
In the field of pharmaceutical packaging, which has almost stringent requirements on quality and safety, the selection of raw materials is the first step to success. Ysa Aluminum is well aware of this and focuses on providing high-performance aluminum foil roll raw materials.
- Focus on high-purity aluminum foil: We focus on the production of high-quality aluminum foil rolls such as 8011 and 8079, and strictly follow the purity requirements of pharmaceutical packaging materials.
- Strict quality control: From raw material procurement to production process (melting, rolling, slitting, annealing), strict quality monitoring of the entire process and multiple nodes is implemented to ensure that the performance of each roll of aluminum foil is stable and reliable. We have advanced online detection equipment, such as X-ray pinhole detection, surface defect detection, thickness online monitoring, etc. and complete laboratory testing capabilities.
- Customized service: According to the specific needs of customers’ pharmaceutical foil production, we can provide 8011 aluminum foil roll products with different thicknesses, widths, states, and surface treatments, and cooperate with the optimization and adjustment of processing performance.
- Compliance and Document Support: We actively obtain and maintain relevant international and domestic certifications, and provide detailed and regulatory-compliant material technical documents, declarations of conformity, material safety data, and factory inspection reports for each batch.
- Stable supply guarantee: A strong production capacity base and perfect supply chain management ensure the stable and timely delivery of customer orders, providing solid support for the continuous production of pharmaceutical foil manufacturers.
8011 aluminum foil roll, as the core substrate of modern pharmaceutical blister packaging sealing foil, silently guards the medication safety of hundreds of millions of patients with its irreplaceable absolute barrier, safe and pure nature, balanced and excellent mechanical properties, and excellent processing adaptability. Its value is far more than a thin layer of metal, but it is the key guarantee for the stable quality of drugs throughout their life cycle from the factory to the hands of patients.
For professional pharmaceutical foil manufacturers, choosing an 8011 aluminum foil roll raw material with excellent performance, stable quality, safety and compliance is the basis for building high-quality pharmaceutical packaging products and the core competitiveness to win market trust. Choosing ysa Aluminum, you choose not only a roll of aluminum foil, but also a commitment to quality and a guarantee of supply chain security.