What Is PVA
PVA film is a water soluble film that can dissolve quickly in water.
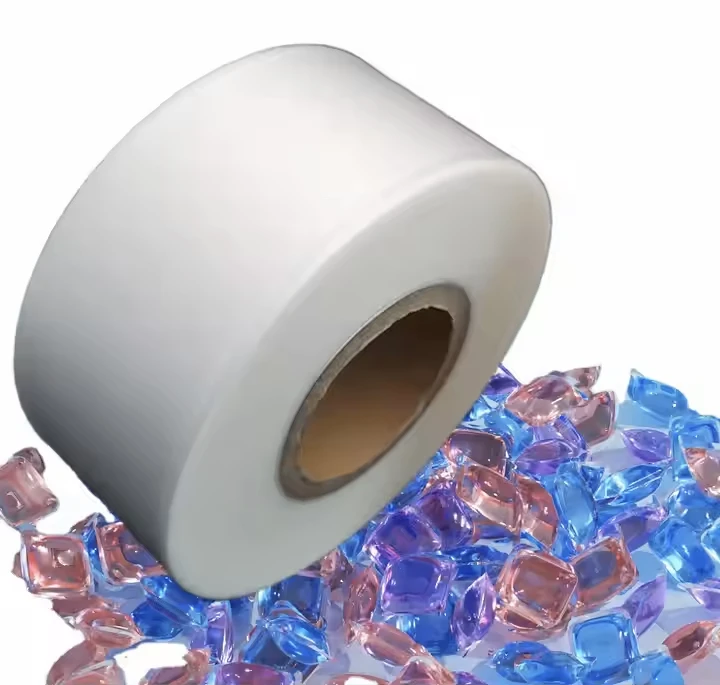
PVA is made of polyvinyl alcohol and is in the form of white powder, flakes, or flocs. It forms a stable colloid in water, and its performance is between that of plastic and rubber. In addition to being used as fiber raw materials, it is also widely used in the production of coatings, adhesives, dispersants, and films. The following are the basic parameters of PVA:
Density | Refractive Index | Moisture Content |
1.26-1.29g/cm³ | 1.52 | 30%-50% |
Is pva Plastic
Yes, PVA (Polyvinyl Alcohol) is a type of synthetic polymer, which is considered a plastic. It is notable for being water-soluble and is used in various applications such as paper coatings, adhesives, and packaging materials.
PVA film has good density, strong adhesion, and a soft and smooth surface. It is non-toxic and harmless to the human body, environmentally friendly, and can be degraded in a short time.
12 Properties Of PVA Film
Environmental Protection
PVA is non-toxic and can be degraded by water and organisms. Dissolving it in water to form a glue that penetrates into the soil can increase the soil’s viscosity, air permeability and water retention, and is particularly suitable for sandy soil reconstruction.
Water Solubility
The solvent of PVA is water, which can be almost completely dissolved in water at room temperature of 20°C.
Strength and Weatherability
PVA film has good toughness, high tensile strength, and the highest tear strength among all types of films. It also has superior biaxial tensile strength, good weather resistance, and long service life.
Transparency and Glossiness
The transparency and glossiness of PVA film are better than other plastic films.
Barrier Properties
PVA film has excellent oxygen barrier properties under dry conditions, and its oxygen permeability coefficient is the lowest among all resin films. PVA film has strong permeability to moisture and ammonia but has excellent barrier properties to other gases. Using PVA can keep the ingredients and smell of the packaged product intact.
Anti-static
Many plastic films have strong electrical charges, but PVA films have almost no static electricity. When using PVA films to package products, static electricity will not cause its plasticity to decrease or static dust to attach.
Printing Performance
PVA film has excellent water color and ink printability and can be used for water transfer printing, such as color printing on irregular surfaces such as glass, ceramics, electrical housings, and automotive parts. At the same time, PVA film has strong polarity and does not require electric spark treatment during printing. It is widely used in special printing industries, such as water transfer film substrates.
Heat Sealability
Water-soluble packaging film has good heat sealing properties and is suitable for resistance heat sealing and high-frequency heat sealing. The heat sealing strength is related to temperature, humidity, pressure, time, and other conditions and is generally greater than 200 g/cm².
Fragrance Retention
PVA film has excellent fragrance preservation and the ability to prevent the sublimation of packaging materials. The use of PVA film for packaging can not only well maintain the fragrance of the packaging materials but also prevent the packaging materials from being affected by external odors.
How to Make PVA
PVA is mainly produced through solution drooling and extrusion-blown film methods.
Tape casting is to mix the raw materials, additives, and solvents in a reactor with ultrasonic or mechanical stirring and then add a release agent, plasticizer, and other functional additives to mix them after they are uniform to obtain a glue solution. Then put it into an insulation kettle for insulation and defoaming. During molding, the glue solution flows from the lower part of the insulation kettle through a pipe to the carrier tape, and the green film layer is formed by the relative movement of the carrier tape and the scraper. The green film layer and the carrier tape enter the drying room together, the solvent evaporates, and the finished film with strength and toughness is obtained.
There are two types of extrusion blown film methods: the wet and dry methods. The following is a detailed description:
The blow molding method for producing PVA plastic packaging film mainly uses polyvinyl alcohol as the matrix and adds water and other additives to form a film through an extrusion blow molding machine.
Wet extrusion blow molding method: The melting point of polyvinyl alcohol is 220°C–240°C. Since it starts to dehydrate and etherify at 160°C and decomposes at 200°C, it is difficult to directly extrude the melt-blown film in terms of technology. Generally, polyvinyl alcohol resin with a water content of 40%–50% is used for extrusion blow molding film.
Dry extrusion blow molding method: After PVA is vacuum dried for 24 hours, it is evenly mixed with a plasticizer and a film-forming agent in a high-speed mixer in a certain ratio and then extruded into granules using a Brabender 225 single-screw extruder with a modified diameter and then subjected to degassing, film blowing, and shaping treatment to obtain the product.